Thermal Cleaning Systems are used for cleaning of spinnerets in Melt-blown nonwoven production line.
► CLEANING PROCESS
Vacuum Pyrolysis Cleaning ⇒ Ultrasonic Cleaning
► THERMAL CLEANING SYSTEMS
Production Line | Thermal Cleaning Systems | |
1.6m (Net Width) | Vacuum Pyrolysis Cleaning Oven Horizental Type, Model: VCH623 or Box Type, Model: VCB2344 |
Ultrasonic Cleaner Chamber Size: 2100X300X250 Ultrasonic Power: 3kW |
2.4m (Net Width) | Vacuum Pyrolysis Cleaning Oven Horizental Type, Model: VCH632 or Box Type, Model: VCB3244 |
Ultrasonic Cleaner Chamber Size: 3000X300X250 Ultrasonic Power: 4.5kW |
3.2m (Net Width) | Vacuum Pyrolysis Cleaning Oven Horizental Type, Model: VCH740 or Box Type, Model: VCB4055 |
Ultrasonic Cleaner Chamber Size: 3800X300X250 Ultrasonic Power: 6kW |
► ELECTRICAL PROCESS HEATER
Production Line | Electrical hot air heater |
1.6m (Net Width) | 240KW |
2.4m (Net Width) | 360KW |
1.6m (Net Width) | 450KW |
► On-site Photo
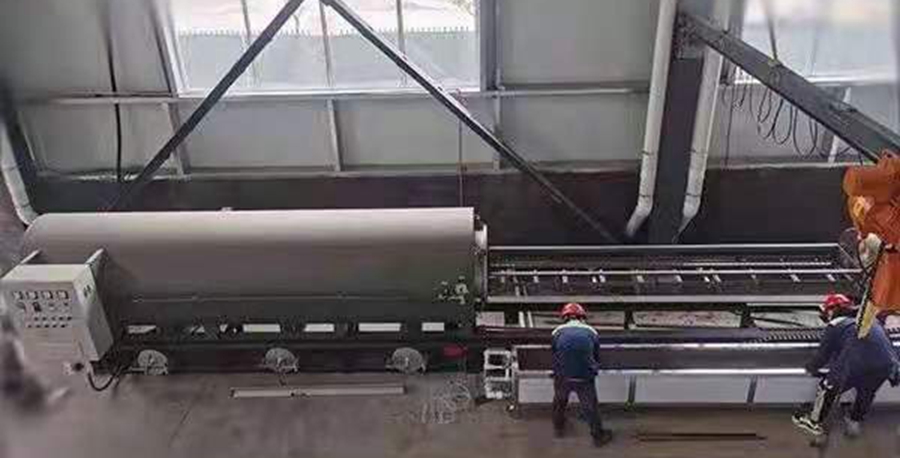
▲ On-site Test
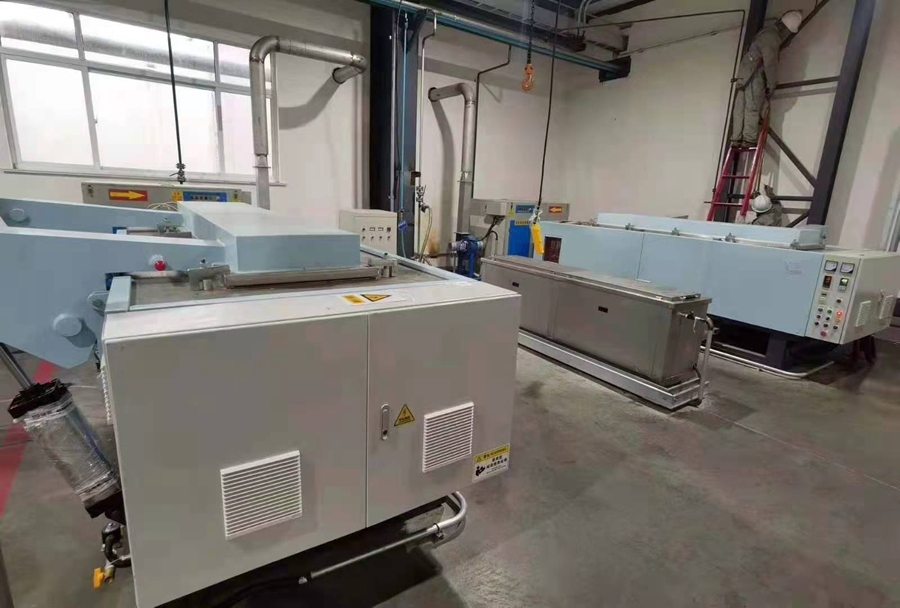
▲ Box Type
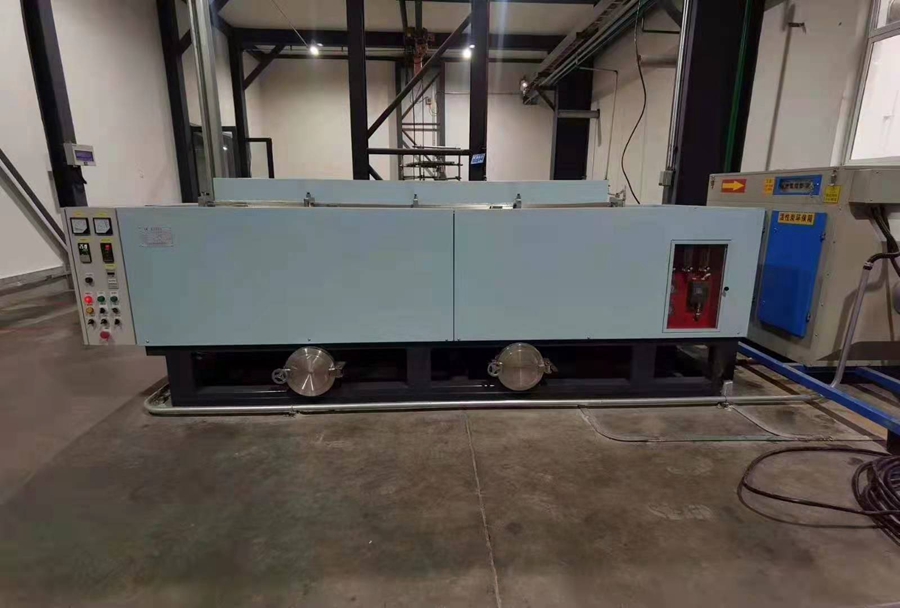
▲ Top Loading
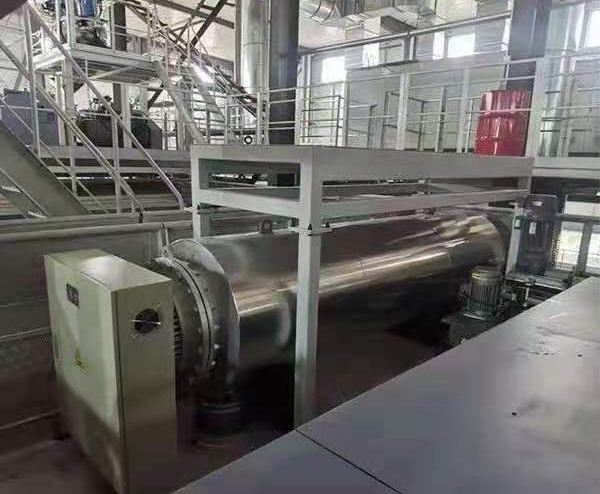
▲ Hot air heater
Brief Description for Melt-blown Production Line
► Composition structure:
Screw extruder > filter > metering pump > heating system -> melt-blown manifold> web former > rewinding
► Production process:
The polypropylene is automatically sucked into the screw extruder by the vacuum feeder, which heats and melts the PP particles into the liquid state. The compressed air from the blower or air compressor and air storage tank is sent to the air heater for heating. The hot air makes the melted liquid polypropylene material ejected from the nozzle to form filaments (the nozzle contains hundreds of small holes) under the pressure. After that, the filaments are ejected horizontally to reach the web former, and then reach the winding equipment.